SCIENZA E RICERCA
Ripensare la produzione di cemento e acciaio per abbattere le emissioni
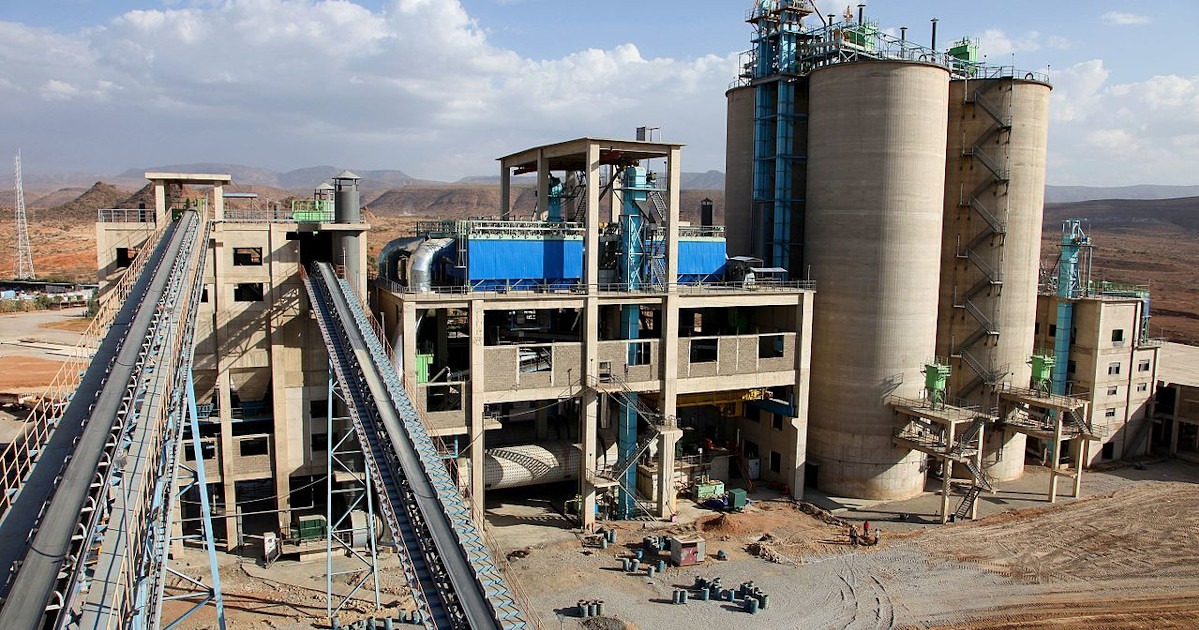
Cementificio in Etiopia – UK Department for International Development
Esiste una serie di settori industriali altamente energivori, le cui emissioni di gas serra che contribuiscono al cambiamento climatico sono difficili da abbattere (in inglese sono detti infatti hard-to-abate). Tra questi vi è la produzione di acciaio, ceramica, carta, vetro, cemento, varie branche dell’industria chimica e le fonderie. Un articolo pubblicato su Nature delinea quali sono le prospettive di decarbonizzazione di due di questi settori industriali, l’acciaio e il cemento, per i quali vengono individuate nove priorità, riportate di seguito.
Efficienza energetica
Innanzitutto è necessario diminuire i consumi complessivi di energia. Un adeguato isolamento termico degli impianti industriali può far risparmiare fino al 26% dell’energia impiegata, caldaie più efficienti fino al 10%, mentre migliori scambiatori di calore possono ridurre del 25% la domanda di energia.
Usare meno cemento e acciaio
Vanno anche diminuiti complessivamente i consumi globali di questi materiali. Dopo l’acqua potabile, il calcestruzzo (ottenuto dal cemento) con cui costruiamo edifici e infrastrutture è il materiale più utilizzato sulla Terra.
Le quantità di cemento che oggi utilizziamo sono troppo alte: in media, 530 kg a persona ogni anno. Lo stesso vale per l’acciaio: 240 kg a persona ogni anno. Secondo il rapporto Material efficiency in clean energy transitions dell’Agenzia Internazionale dell’Energia, architetti e ingegneri possono ridurre di circa un quarto queste quantità annuali con piccoli accorgimenti e buone pratiche, come ad esempio l’impiego di modelli computazionali più accurati in fase di progettazione, che permettano di ottimizzare l’impiego dei materiali. Anche l’industria automobilistica potrebbe sostituire l’acciaio con alluminio, in alcune componenti.
Ripensare la produzione dell’acciaio
Quella dell’acciaio è un’industria altamente energivora e ad alte emissioni. Per trasformare chimicamente i minerali ferrosi in ferro metallico servono temperature al di sopra dei 2.300°C, ottenute bruciando coke, un derivato del carbone. Questo procedimento produce sia monossido di carbonio sia anidride carbonica.
Il ferro fuso così ottenuto viene poi raffinato in acciaio, spesso in fornaci alimentate a carbone, più raramente in forni elettrici ad arco, la cui elettricità è però spesso prodotta tramite centrali termoelettriche che bruciano gas o altri combustibili fossili. Per il futuro si mira a impiegare più forni elettrici ad arco la cui elettricità dovrà venir prodotta in modi più sostenibili, anche le quantità richieste sono proibitive: per ogni tonnellata di acciaio vengono emesse 1,8 tonnellate di CO2.
Esistono procedimenti, come il DRI (Direct Reduced Iron), che evitano l’impiego di coke: al suo posto si può utilizzare l’idrogeno, riducendo fino a 50 kg le quantità di CO2 emessa per tonnellata di acciaio prodotta (una riduzione delle emissioni del 97%).
Il problema è che questo procedimento richiederebbe moltissimo idrogeno: bisognerebbe passare dai 60 milioni di tonnellate di idrogeno annuali di oggi a 135 milioni di tonnellate. Solo una piccolissima parte dell’idrogeno però oggi è prodotta in modo sostenibile (l’idrogeno verde prodotto dall’acqua con elettrolizzatori alimentati da fonti rinnovabili): la stra grande maggioranza dell’idrogeno viene invece ottenuto dal metano, emettendo CO2. Europa, Cina e Australia hanno in programma alcuni esperimenti pilota, dal 2025, di produzione industriale di acciaio con l’impiego di idrogeno. Mano a mano che si diffonderanno gli elettrolizzatori, l’idrogeno verde costerà sempre di meno.
Ripensare la produzione del cemento
Il cemento più comune al mondo (noto come cemento Portland) viene prodotto a partire dalla calcinazione del carbonato di calcio (calcare), un processo che avviene a 850°C e che permette di ottenere calce viva e anidride carbonica. La calce viva viene poi combinata con sabbia e argilla a 1450°C per ottenere un materiale noto come clinker, il quale viene macinato e al quale vengono aggiunte altre componenti come il solfato di calcio (gesso) per ottenere il cemento. Per ogni tonnellata di cemento prodotto vengono emessi dai 600 agli 800 kg di CO2: la maggior parte viene prodotta durante il processo di calcinazione, il resto deriva dai combustibili fossili utilizzati per alimentare i processi.
Esistono modi per ottenere il cemento senza partire dalla calcinazione del calcare, ma sono poco diffusi e poco commercializzati perché non hanno le stesse proprietà del cemento Portland. Al posto del clinker i ricercatori stanno sperimentando nuovi materiali, come il ferro riciclato dalla produzione di acciaio DRI nei forni elettrici ad arco. Una soluzione interessante è il cemento LC3 (Limestone Calcined Clay Cement) che è in grado di ridurre l’uso di clinker del 50%, evitando le emissioni connesse alla sua produzione. Alcune aziende in Francia e in Germania (LafargeHolcim e Heidelberg Cement) ne fanno già uso.
Sostituire i combustibili fossili
Sebbene sia auspicabile sostituire l’uso di combustibili fossili con soluzioni più sostenibili come le biomasse, ci sono delle notevoli difficoltà. Una è il consumo di suolo agricolo per produrre biomasse a sufficienza. Per quanto riguarda il cemento invece sarebbe possibile incenerire i rifiuti solidi urbani nelle fornaci e utilizzare le ceneri per fare il clinker, abbassandone l’impatto ambientale. Nel Messico e nel Regno Unito esistono già aziende che adottano questi metodi.
Cattura e stoccaggio della CO2
Secondo gli autori del commento su Nature, la cattura e lo stoccaggio dell’anidride carbonica (CCS – Carbon and Capture Storage) sarà uno strumento fondamentale per ridurre le emissioni del settore siderurgico e cementifero. La tecnologia però non è ancora diffusa e deve risolvere ancora diverse problematiche. Ad esempio, per essere catturata in modo efficace, è necessario che la CO2 sia pura al 99,9%, altrimenti lievitano i costi economici ed energetici per comprimerla e immagazzinarla. I flussi di CO2 emessi dall’industria di acciaio e cemento invece sono puri solo al 30%, perché contengono molto vapore acqueo e azoto.
Stoccare CO2 nel cemento
Esistono altri modi per catturare la CO2. Per produrre calcestruzzo occorre aggiungere sabbia, acqua e ghiaia al cemento. “L’acqua innesca reazioni che induriscono il materiale. Aggiungere CO2 può rendere ancora più forte il cemento. Se fosse solo l’1,3% del peso del calcestruzzo, la durezza del materiale aumenterebbe del 10%. Questo ridurrebbe al contempo la quantità di cemento utilizzato (e le emissioni di conseguenza) di circa il 5%”. I ricercatori stanno lavorando a soluzioni anche più performanti.
Cemento e calcestruzzo sono anche in grado di assorbire anidride carbonica dall’aria convertendo le proprie componenti di calcio in carbonato di calcio (calcare). In linea di principio, fino a metà delle emissioni generate durante la produzione del cemento possono venire riassorbite, sostengono gli autori. Tuttavia i materiali dovrebbero venire macinati a fine vita in modo da rendere più piccole le particelle di calcestruzzo e permettere una migliore diffusione della CO2. Questo procedimento richiede dispendio energetico ed economico. Il governo britannico e il Global Carbon Project stanno tentando di quantificare questa capacità di assorbimento nel loro carbon budget. Secondo gli autori del commento tuttavia, è presto per dire che questo metodo di assorbimento della CO2 potrà sostituire le tecnologie di CCS.
Riciclare acciaio
Oggi un quarto della produzione di acciaio avviene a partire da frammenti di acciaio riciclato. Entro il 2050 questa quota deve raddoppiare, comportando una riduzione del 25% delle emissioni. Dovrà migliorare la selezione dei pezzi da riciclare, rendendo più facilmente removibili frammenti di altro materiale, come ad esempio fili di rame, che altrimenti abbassano progressivamente la qualità dell’acciaio.
Sostenere il cambiamento
Aumentare la quantità di idrogeno nella produzione dell’acciaio e il CCS nella produzione di cemento comporta costi notevoli. Di conseguenza queste soluzioni a basse emissioni (potenzialmente) sono economicamente ancora poco vantaggiose: questo è un problema soprattutto nei Paesi in via di sviluppo. Lo schema di scambio delle emissioni dell’Unione Europea (ETS – Emission Trading System) può rendere economicamente più vantaggiose queste soluzioni, ma non è abbastanza: servirebbero anche incentivi dei governi nazionali.
Ad esempio, l’acciaio costa in genere 600 dollari a tonnellata; un acciaio a basse emissioni costerebbe dal 20% al 40% in più, il che significa che dovrebbe avere incentivi per 240 dollari a tonnellata. Secondo gli autori, simili incentivi costerebbero all’Unione Europea 200 miliardi di dollari in 10 anni. Andrebbe dunque organizzata anche la filiera economica di questi materiali: per andare nella giusta direzione i costi non andrebbero fatti ricadere sui consumatori, ma sui produttori, fino a un assestamento del mercato.